Our client bought an older 2 story office building in great need of a face lift. We came up with a simple modern vision, the back lot is a P zone and in need of a zone change for housing. We are still working to determine if that will be acceptable in a short time frame. A new 16 unit Live Work loft design is what we suggested.
Office Tenant Improvements
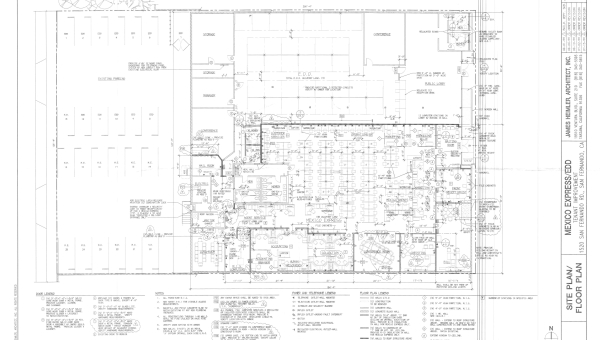
we started working for Mexico Express which over time switched their name to Sigue. We worked on their first relocation of all their office tied with a temporary use for the Social security Administration. Our design maintained a flexibility for future growth. Then the property across the street was proposed as a 3 story new large corporate facility while streets were being realigned within the City of San Fernando.
This Tenant Improvement for a Realtor’s office is located in an old retail building with sloping ceilings. The parking in the rear of the site and the entry had a few access issues that needed resolving. We broke up the linear space with angle walls to help define spaces and break up the length of the open floor plan along one side of the space. The ceilings were also used to define space. The entry has a low hung ceiling defining that zone. We worked with exiting conditions without having to reduce any design issues that we could work around. The angled walled offices work better as spaces of use rather than just a rectangular office or conference room. Our clients are very happy with the results.
Easton Bell was combining five divisions from all over the country and uniting them into a new, 80,000 S.F., corporate headquarters. The corporate headquarters was designed with the company’s youthful sporty atmosphere and staff in mind. The building has many departments, each with their own communal spaces. We reconfigured uses for a 4-story building and studied the merchandizing of their company image and how their entry spaces could be redesigned. This project involved buildings on both sides of a street and each area had to be programmed, designed, and incorporated into the design. The corporate headquarters included the company’s training facilities, research and development office, executive offices, ice skating product-testing rink, and accounting offices. We incorporated these mostly open departments so that they worked together in a flexible manner. We maximized all space planning opportunities, as the number of departments, people and space we were allowed to work within was tight. We maximized circulation by moving existing exit doors. A design studio was converted to a test ice rink for product development. We began this project with a Silver LEED certification as our goal. To achieve this certification we incorporated post industrial and post consumer materials such as: fly ash as an aggregate; ceiling tiles; plumbing fixtures; doors; work stations; fabrics; glass; metals; and harvested wood. The use of natural lighting ( from walls to skylights), window films, and high rating insulation would lower energy consumption, and on-site recycling and use of regional materials would reduce environmental impact. The over-all post consumer content considered amounted to 80% of all materials needed. Low water consumption plumbing fixtures were specified. Showers and bike storage was included. To achieve optimal design, value engineering and sustainability, we worked closely with all consultants on the project. They continue to use us for tenant improvements and we are discussing the future possibility of designing a permanent, larger corporate headquarters.
The two story, 50,000+SF industrial tenant improvement project (corporate office/production/sales); is a design/coordination through construction administration. The building is the new corporate headquarters for the company. The estimated cost is near $2 million. The construction costs are approximately $2 million under a design/built flexible program.
We designed improvements for the first/second floors, rehabilitation roof, and parking in pursuit of Silver LEED certification. We assisted in applying for this certification and in the coordination of consultants and owner for the certification process. The building will have a reflective roof coating; HVAC units with high energy efficiency; vertical duct work to the floor for low air circulation; denim insulation; energy efficient light fixtures with motion sensors; and recycled furniture. Our responsibilities include design, construction documents, coordination, expediting, and construction administration.